Monitoring and regulation
Data logging
Commissioning, validation and maintenance
Flawless air quality management, guaranteed
In clean rooms, avoiding contamination depends on irreproachable indoor air quality management. That’s why, for 45 years, Sauermann has been putting the best of its R&D expertise to work for these critical environments, which are subject to particularly stringent standards. Our aim, as always, is to manufacture the best products and to deliver an impeccable service to industry professionals.
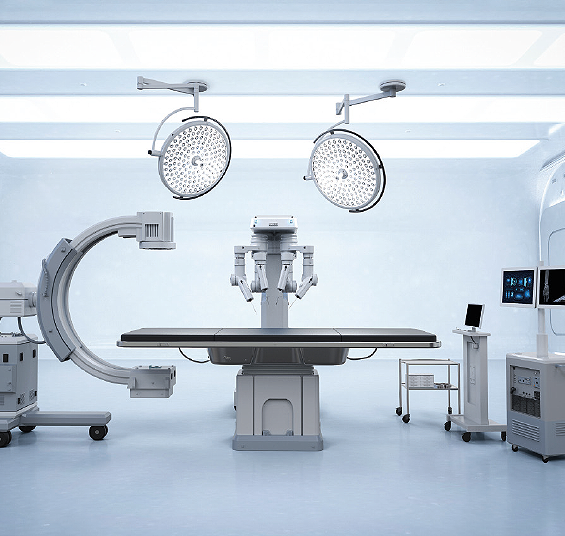
At the cutting edge across all sectors
Effective ventilation system management is essential in any sector where airborne particles such as dust, bacteria, viruses, micro-particles and aerosols can disrupt operations. At Sauermann, we work hand in hand with our partners in industries ranging from advanced electronics and pharmaceuticals to aviation, hospitals and biotechnology .
Spanning every aspect of metrology
Sauermann harnesses the full breadth of its metrology expertise to help clean rooms adhere to stringent standards, from constant monitoring to ad hoc tests and everything in between: air flow balancing, calibration, and testing and repairing of measurement instruments for pressure, humidity, temperature, air velocity and air flow, CO2 concentration and other parameters.

The jewel in our crown
Controlled-environment buildings demand the very best monitoring and control instruments – certified and setting the gold standard for reliability. Sauermann has its own manufacturing facilities, in-house ISO 17025:2017 accredited laboratories for hygrometry and temperature in Montpon, and a team of onsite technicians with the requisite expertise, all backed by a 45-year track record in metrology. That’s why our customers rely on us to supply flawless measurement instruments, and to be there by their side for the long term.
A world of standards and regulations
Clean rooms undergo qualification and constant re-qualification to strict standards, requiring advanced measurement instruments to make sure they meet the grade. In order to comply with these GxP quality and traceability regulations, they must keep records of the conditions in which they operate, in accordance with Good Manufacturing Practice (GMP) standards.
EN ISO 14644-1 |
Maximum permitted concentration (Particle per m2 ) | |||||
---|---|---|---|---|---|---|
Class | ≥ 0.1 μm | ≥ 0.2 μm | ≥ 0.3 μm | ≥ 0.5 μm | ≥ 1.0 μm | ≥ 1.0 μm |
ISO 1 | 10 | |||||
ISO 2 | 100 | 24 | 10 | |||
ISO 3 | 1 000 | 237 | 102 | 35 | ||
ISO 4 | 10 000 | 2 370 | 1 020 | 352 | 83 | |
ISO 5 | 100 000 | 23 700 | 10 200 | 3 520 | 832 | |
ISO 6 | 1 000 000 | 237 000 | 102 000 | 35 200 | 8 320 | 293 |
ISO 7 | 352 000 | 83 200 | 2 930 | |||
ISO 8 | 3 520 000 | 832 000 | 29 300 | |||
ISO 9 | 35 200 000 | 8 320 000 | 293 000 |
Fighting contamination with precision
In clean rooms, monitoring and control measurements rely on extremely narrow margins, especially when it comes to differential pressure. Each room has to be kept slightly above or below the pressure outside in order to prevent the risk of atmospheric contamination. Sauermann’s instruments are designed to provide the measurement accuracy and resolution that these demanding applications require.
Air change rate is the speed at which all the air inside a room is replaced by the ventilation system. To calculate this rate (ACR), expressed per hour, the airflow rate of each inlet of the ventilation system is divided by the total volume of the room concerned.
Mathematically is expressed by this simple equation:
ACH = Q/V
ACH = number of air changes per hour
Q = air flow
V = space volume
The pressure differential between adjacent cleanrooms or clean zones of different cleanliness level should lie typically in the range of 5 Pa to 20 Pa, to allow doors to be opened and to avoid unintended cross-flows due to turbulence.
Source: ISO 14644-4; Cleanrooms and associated controlled environments Part 4: Design, construction and start-up
