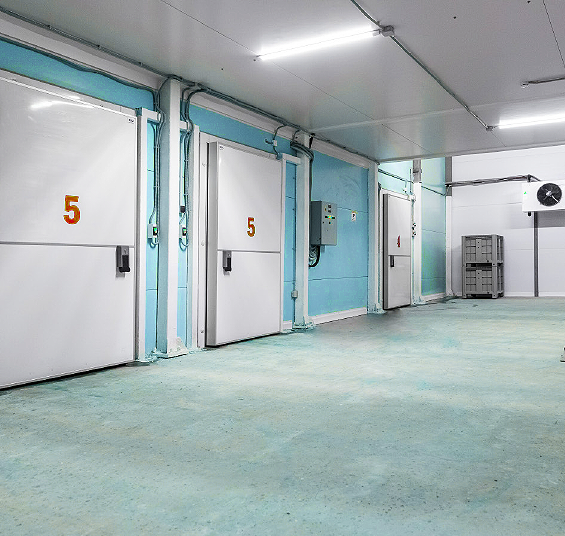
Refrigeration is among the most essential industries worldwide: it stands at the very foundation of our food supply due to the importance of the cold chain, it is also at the basis of the production processes for countless sensitive and vital products, such as drugs, vaccines and other pharmaceuticals. Refrigeration is also at the crossroads of major concerns: food safety on a large scale, as well as the preservation of our environment.
That’s why manufacturers and operators of refrigerators and freezers face increasing demands on operational safety and environmental protection. Pressure, temperature, superheating and subcooling of a refrigeration system must be regularly checked to ensure it functions smoothly, safely and efficiently.
The extensive international standards and regulations on the tightness of refrigerant systems are continually being revised. As the most used refrigerants are greenhouse gases with high global warming potential (commonly known as GWP), the regulations are becoming stricter. That’s why every part of the cold chain must be frequently tested: production installations, refrigeration plants, freezers, refrigerators, refrigeration units, etc.
Temperature and pressure
Temperature and pressure
The two most important parameters for the maintenance of refrigeration systems are temperature and pressure, as they are the key to verifying the proper functioning of the cooling process.
The advent of digital technology means huge quality improvements when it comes to the adjustment of refrigeration systems or heat pumps. Digital manifolds provide high-precision temperature and pressure measurements, determine subcooling and superheating, but also enable reliable evacuation of the system through accurate vacuum measurement.
Si-RM13
This Si-RM13 combines the sturdiness of the analog manifold with digital smart wireless temperature and pressure probes.
This premium package includes a traditional 2-channel analog manifold body (by-pass type) with flexible hoses and a durable block made of anodised aluminum.

Data logging
Data logging
Data logging is an essential activity when monitoring the operation of a cooling system over an extended period of time and the temperature behavior within a cold store. Therefore, it is the main tool to ensure that the cold chain has not been broken during storage and transportation.
The recording of temperature and humidity data within a refrigeration or freezing area makes it possible to certify that the cold chain has been maintained throughout its most sensitive sections, primarily the transport of thermal sensitive goods like vaccines.
Given the massive health hazard involved in breaking the cold chain, data loggers enable the food and pharmaceutical industries to guarantee compliance with the strict quality requirements set out in international standards.
Leak detection
Leak detection
Refrigeration systems can severely suffer from refrigerant gas leaks. Also, most refrigerants are powerful greenhouse gases and can seriously harm the environment. For this reason, it is extremely important to be able to easily locate any leak in order to quickly fix the impacted portion of the gas circuit. Searching for and finding gas leaks can be very difficult. Fast professional leak detectors are essential to precisely locate the smallest leaks in a refrigerant circuit.
Products and accessories
Videos
Over 800 m2 of laboratory space
Our experts provide maintenance, adjustment and calibration services for our measurement instruments.
After-sales service
Our technicians maintain and repair your devices right where they’re made.
Over 20 patents
Including our oscillating piston pump technology and the foldable frame system found on our DBM 620 air flow meter.